Metallurgy
From extraction to production, metallurgy and metallography are used to examine the microscopic mechanisms that affect the behaviour of metals, their composites and alloys. A well manufactured material can be made more resistant to virtually any source of potential failure, including corrosion, stress and creep – all of which are crucial considerations for the use of metals and alloys in manufacturing and engineering. To achieve this, however, metallurgists must contend with a host of complex factors, both naturally occurring and those resulting from engineering processes, which can alter the physical properties of metals and ultimately, their industrial applications. Just as the macroscopic properties of metals are tested using instruments capable of measuring their hardness, tensile strength and compressive strength, analysis of a metal’s microstructure is carried out using a combination of general and specialist microscopy techniques.
Grain Sizing
Correct grain size is crucial to material microstructure and in obtaining correct physical and mechanical characteristics for a wide range of materials such as metals, plastics, mineral and composites in the engineering, construction, medical device, semiconductor/electronic and many other sectors. Fine grained steels, for example, provide strength while coarse grained steels are more easily machined. The analysis of grain size is used as a quality control tool to ensure that materials are manufactured to specification and are fit for purpose. Grain size analysis is also used diagnostically to understand material failures in research and development settings and in on-going quality control. The process of grain analysis in quality control must be performed to established standards available from organizations such as ASTM and JIS.
Cast iron nodularity and flake analysis
Cast iron is used widely in the automotive and heavy equipment industries for structural components such as engine, brake, suspension, and steering parts. Cast iron is formed by adding carbon (graphite) to steel. The carbon can precipitate in different forms, for example, in nodules or spherulites (in ductile iron), in a vermicular or flake form (gray iron) or in compacted aggregates (malleable iron). The proportion of nodules, their size and their distribution is a key factor in determining the properties of ductile iron, the greater the proportion of nodules, the greater the strength and ductability. Other properties such as ductility and impact properties are also determined by the structure of the matrix. The matrix, for example, consists of varying proportions of ferrite and pearlite. The greater the amount of pearlite present, the greater the strength and hardness. The characteristics of cast iron are formed during solidification and once solid cannot be changed through further heating.
Metal manufacturing
Quality control is paramount in the metal manufacturing industry as lapses in quality can lead to serious performance and safety impairments. Quality control measures range from ensuring key dimensions are within tight specifications to other criteria such as checking surface finish and grain/crystal size which can be vitally important since they can have a dramatic effect on quality and performance.
Since the tensile strength of metals is inversely proportional to grain or crystal size, controlling and checking that the correct size is achieved during the manufacturing process is crucial in the manufacture of components such as bearings and crankshafts.
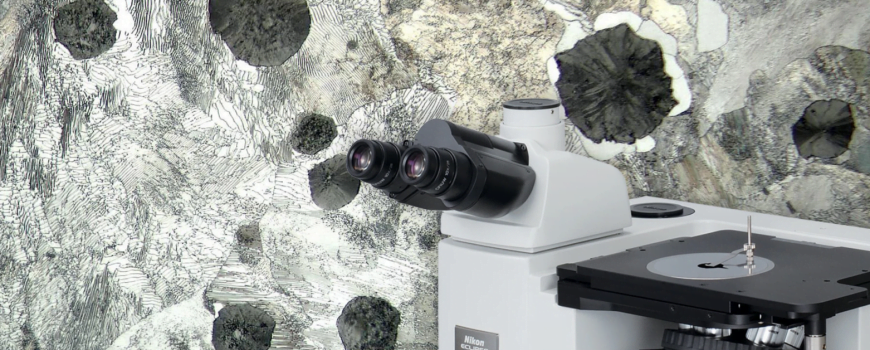